Technology

Which type of molding process is right for your application?
There are a number of factors to consider when determining the type of molding process required. Some of these include:
Rubber Compression Moulding
Compression Moulding is the original production method for moulding rubber. It is ideal for low to medium production volumes and is a particularly useful molding process for molding gaskets, seals, O-rings, and large, bulky parts. It is a widely used, efficient and economical production method for many products, particularly low production volumes of medium to large parts and higher cost materials.
Processes
Compression molding involves taking rubber compound or mixed raw material and making “pre-forms” that are close to the shape of the end product. These shapes are then loaded, typically by hand, into an open mold. The mold is closed, the rubber cured, and then de-moulded.
Compression molding can be cost effective if one or more of the following is true:
Processes
Compression molding involves taking rubber compound or mixed raw material and making “pre-forms” that are close to the shape of the end product. These shapes are then loaded, typically by hand, into an open mold. The mold is closed, the rubber cured, and then de-moulded.
Compression molding can be cost effective if one or more of the following is true:


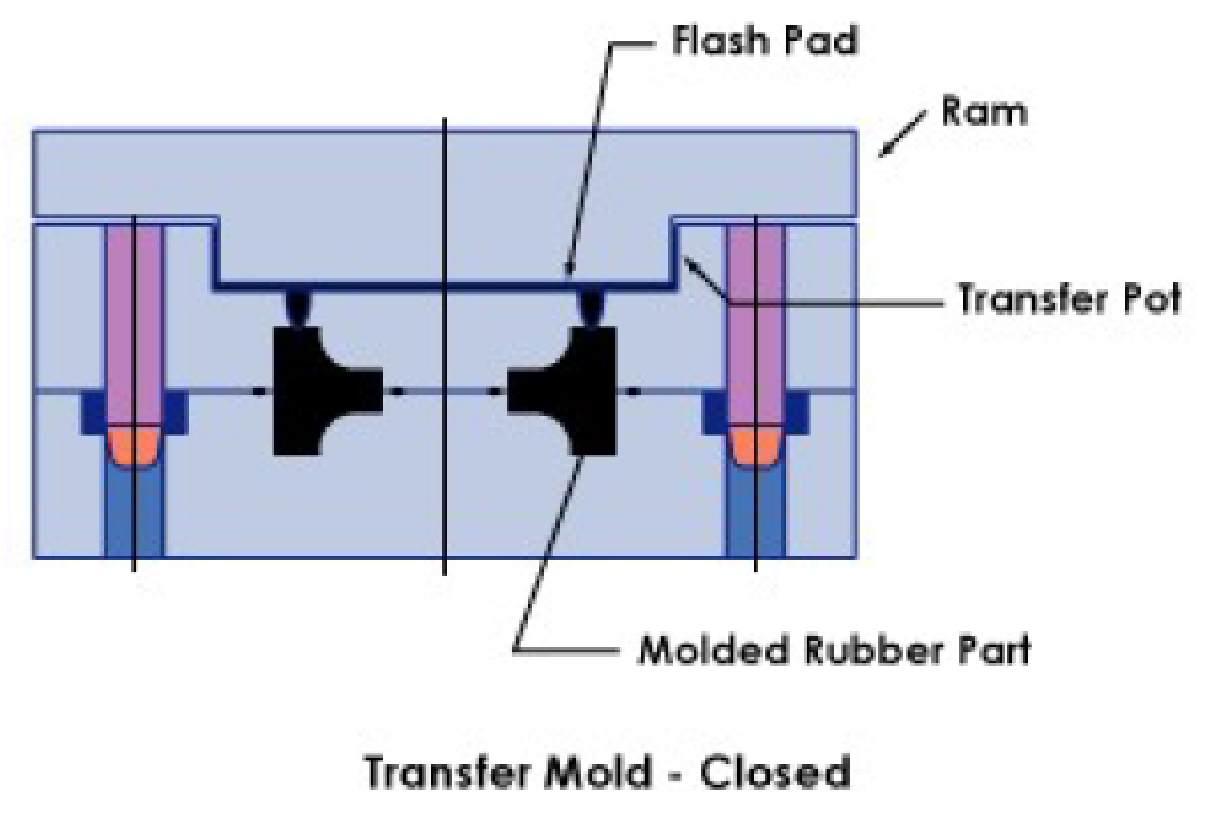
Rubber Transfer Moulding
Transfer Molding combines the advantages of injection molding with the ease of compression molding. Rubber transfer molding is an ideal process for molding parts that require multiple cavities, intricate parts that require a closed mold, bonding rubber to metal parts and if the geometry of the part might cause mold cavities to trap air.
Processes
Similar to compression molding, transfer molding requires secondary raw material preparation into “pre-forms” that are loaded into a “pot.” When the mold is closed, a “piston” compresses the rubber in the “pot” and forces it through holes or sprues into the cavity to fill the part cavity.
The advantages of transfer molding over compression molding can include:
Processes
Similar to compression molding, transfer molding requires secondary raw material preparation into “pre-forms” that are loaded into a “pot.” When the mold is closed, a “piston” compresses the rubber in the “pot” and forces it through holes or sprues into the cavity to fill the part cavity.
The advantages of transfer molding over compression molding can include:
The primary disadvantage is increased waste; the “flash pad” or rubber left in the pot after transfer is typically cured and has to be discarded.
Injection Moulding
Injection molding of rubber was originally an offshoot from the plastics industry in the early 1960s. After overcoming the initial issues of temperature, (plastics are cooled when molding and rubber is heated) and pressure (rubber injection molding requires significantly more pressure per square inch of cavity surface), the process has become an efficient way to mold rubber in many cases.
There are 3 main types of rubber injection molding:
There are 3 main types of rubber injection molding:
Organic Rubber Injection
Organic rubber injection starts with more efficient material preparation. The material is mixed, and then stripped into continuous strips and fed into a screw which charges a barrel as needed with a pre-defined amount of material. When the mold is closed, the material in the barrel is injected into the mold cavities and cured. Benefits of injection molding include:
Liquid Injection Molding (LIM) or (LSR) Injection
is the process where a two part liquid silicone compound (A & B parts) are delivered at a fixed ratio into a static mixer. The LSR mixture blends with a platinum cure system and is delivered into the injection unit where it is injected through a runner and gate system into the closed mold until cured. At the end of the cycle the parts are removed or ejected from the cavities and the next cycle begins. Benefits of LIM molding include:

